Overview
I have always believed that swerve drivetrains are the best for robotics competitions that require mobility and are limited when it comes to robots damaging each other. Due to this, I believe that swerve drivetrains are viable for FTC. Entering high school, these drivetrains were a specialty that a majority of students were unable to access. However, when I started college I wanted to change this for teams all over the world. This is why I started to produce compact swerve drivetrains to start a business selling them to teams at affordable prices.
This project is still being worked on
First Prototype
When designing the prototype we made sure to make the pod as small as possible. Our module is under 4inx4inx4in making it one of the smallest ever made. We manufactured and assembled a drivetrain using these modules to see if it is viable. The pod is inside the moduel and consists of 3D-printed structural parts that hold shafts, gears, and bearings in place. These shafts are linked to motors for pod rotation and movement. Each model consists of one pod, one motor, and one servo. Mechanically the chassis works but the code could be better. The main issue is that these pods are extremely expensive to produce and since we need 4 of them for a drivetrain these will not be viable for mass production. Each pod will cost 400 dollars and a whole chassis will be around 1300.
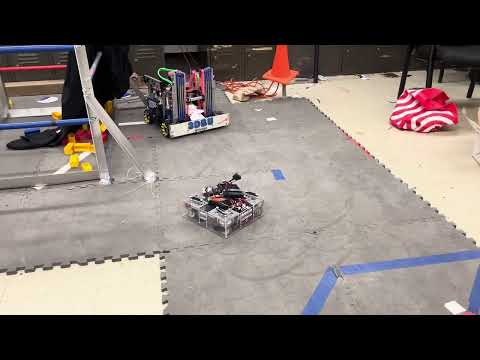
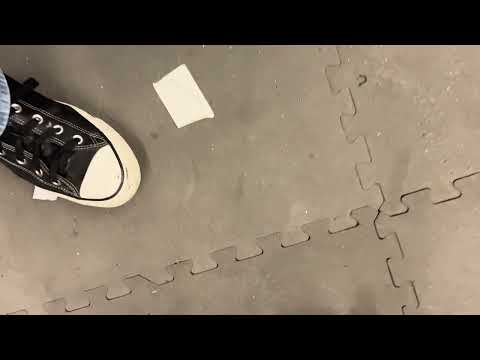

Second Prototype
After creating a robot using the original design we noticed many issues that will be tackled with this new design. The first issue we noticed was how expensive the modules are. We solved this issue by using generic parts on marketplaces like ali-express and Amazon by cutting the total number of custom parts. By getting generic parts we had to increase the size of the module by less than a quarter inch in height. We also disliked the way the module was shaped. We changed it from an L-shape to a rectangle. Finally, we changed the module's hole pattern to fit the Gobilda, rev, and Andymark build-systems.


